Examine This Report on Alcast Company
Table of ContentsAlcast Company - The FactsThe Of Alcast CompanyThe Basic Principles Of Alcast Company An Unbiased View of Alcast CompanyEverything about Alcast CompanyMore About Alcast Company
The subtle difference hinges on the chemical content. Chemical Comparison of Cast Aluminum Alloys Silicon promotes castability by decreasing the alloy's melting temperature and improving fluidity throughout casting. It plays an essential function in allowing complex molds to be filled up accurately. Additionally, silicon contributes to the alloy's strength and wear resistance, making it useful in applications where resilience is vital, such as auto components and engine parts.It also improves the machinability of the alloy, making it simpler to refine right into completed items. This way, iron contributes to the total workability of light weight aluminum alloys. Copper boosts electrical conductivity, making it helpful in electrical applications. It additionally boosts rust resistance and contributes to the alloy's total stamina.
Manganese contributes to the stamina of aluminum alloys and enhances workability (Casting Foundry). It is commonly used in wrought aluminum products like sheets, extrusions, and profiles. The existence of manganese help in the alloy's formability and resistance to splitting during manufacture procedures. Magnesium is a lightweight element that provides strength and impact resistance to aluminum alloys.
Not known Facts About Alcast Company
It enables the manufacturing of light-weight parts with outstanding mechanical buildings. Zinc enhances the castability of light weight aluminum alloys and assists regulate the solidification procedure during casting. It improves the alloy's stamina and firmness. It is typically discovered in applications where complex shapes and fine details are required, such as decorative castings and particular vehicle components.
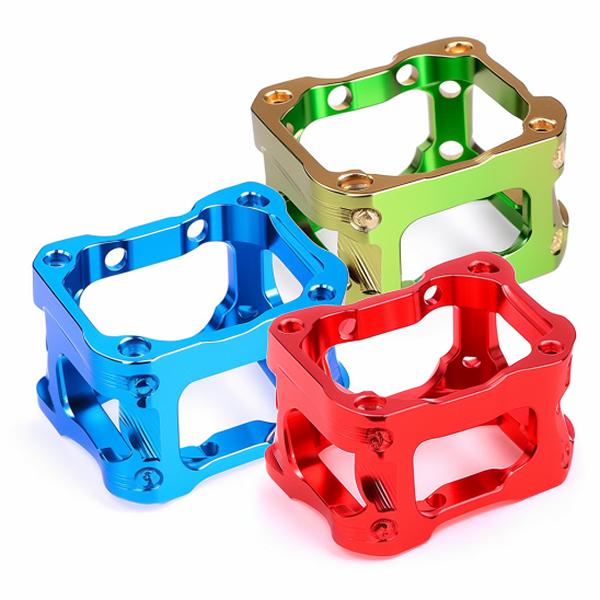
The primary thermal conductivity, tensile toughness, return toughness, and prolongation differ. Amongst the above alloys, A356 has the highest thermal conductivity, and A380 and ADC12 have the lowest.
Some Known Incorrect Statements About Alcast Company
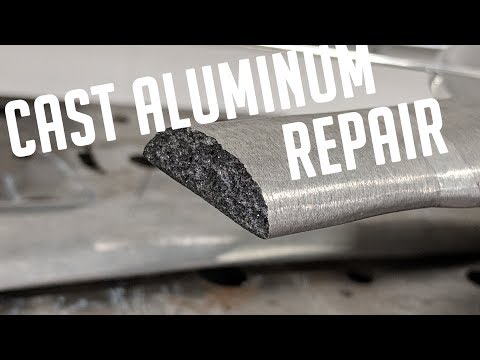
In precision spreading, 6063 is appropriate for applications where complex geometries and top notch surface finishes are vital. Examples include telecommunication rooms, where the alloy's superior formability allows for smooth and cosmetically pleasing styles while preserving structural integrity. Similarly, in the Lights Solutions industry, precision-cast 6063 components create stylish and effective lighting fixtures that call for elaborate forms and great thermal efficiency.
It causes a better surface area coating and better rust resistance in A360. Additionally, the A360 shows remarkable prolongation, making it perfect for complex and thin-walled elements. In accuracy spreading applications, A360 is well-suited for markets such as Customer Electronics, Telecommunication, and Power Tools. Its boosted fluidness allows for elaborate, high-precision parts like mobile phone casings and communication tool real estates.
Examine This Report on Alcast Company
Its special residential or commercial properties make A360 a valuable selection for accuracy casting in these markets, enhancing product longevity and top quality. Light weight aluminum alloy 380, or A380, is a commonly utilized spreading alloy with several distinct qualities. It uses exceptional castability, making it a suitable option for accuracy spreading. A380 displays great fluidity when molten, making sure detailed and comprehensive mold and mildews are accurately reproduced.
In official website accuracy spreading, aluminum 413 radiates in the Consumer Electronic Devices and Power Tools markets. It's generally made use of to craft intricate parts like mobile phone real estates, camera bodies, and power device casings. Its accuracy is impressive, with tight resistances up to 0.01 mm, making certain flawless product setting up. This alloy's exceptional corrosion resistance makes it an exceptional selection for outdoor applications, making certain long-lasting, durable products in the discussed markets.
Alcast Company Can Be Fun For Everyone
As soon as you have actually chosen that the aluminum die casting procedure is ideal for your project, an essential following action is deciding on the most ideal alloy. The aluminum alloy you pick will considerably influence both the spreading process and the residential or commercial properties of the end product. Due to this, you have to make your decision thoroughly and take an educated technique.
Establishing the most suitable light weight aluminum alloy for your application will suggest weighing a broad array of characteristics. The very first group addresses alloy attributes that influence the manufacturing procedure.
Our Alcast Company PDFs
The alloy you select for die casting straight affects numerous aspects of the casting procedure, like exactly how simple the alloy is to collaborate with and if it is prone to casting flaws. Hot fracturing, additionally referred to as solidification cracking, is a normal die casting flaw for light weight aluminum alloys that can lead to internal or surface-level rips or splits.
Certain aluminum alloys are more at risk to warm cracking than others, and your option must consider this. Another usual issue discovered in the die casting of aluminum is pass away soldering, which is when the actors sticks to the die wall surfaces and makes ejection hard. It can damage both the actors and the die, so you must look for alloys with high anti-soldering properties.
Rust resistance, which is already a noteworthy feature of light weight aluminum, can vary significantly from alloy to alloy and is a necessary particular to take into consideration depending on the environmental conditions your item will be subjected to (aluminum casting company). Put on resistance is an additional property commonly sought in light weight aluminum products and can set apart some alloys